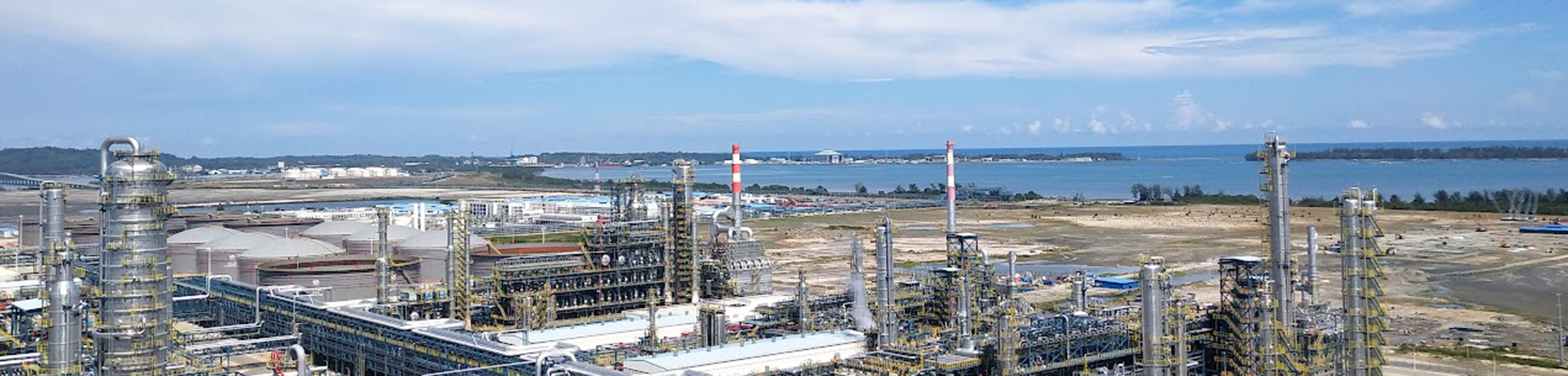
Heat Treatment Services
Heat Treatment Services
Pre-Heat Treatment
Pre-heat treatment in NDT involves applying controlled heat to metal components before welding to ensure they are within a specific temperature range. This process reduces the cooling rate of the weld pool, minimizes residual stresses, and drives out moisture and hydrogen from the weld area, thus preventing hydrogen-induced cracking. This process uses thermocouples, electrical resistance heating elements, or induction coils to achieve a specified temperature range on both sides of the weld joint. Maintaining proper preheat and interpass temperatures is essential to control the cooling rate of the weld puddle, drive out moisture, and prevent hydrogen build-up and potential cracking.
This ensures a softer, less brittle microstructure in the weld metal and Heat Affected Zone (HAZ), facilitating the diffusion of hydrogen during welding. Pre-heat treatment is essential in industries such as oil and gas, construction, shipbuilding, where welding thick or high-strength steels is common. By improving weld quality, enhancing mechanical properties, and ensuring compliance with industry standards, pre-heat treatment plays a crucial role in achieving reliable and defect-free welds in critical structures and components.
Post Weld Heat Treatment
Post Weld Heat Treatment (PWHT), also known as stress relieving, is applied after welding to address stresses caused by high temperatures and rapid cooling. This process involves applying controlled heat treatment to welded components or structures after the welding process is completed. The purpose of PWHT is to relieve residual stresses, improve the mechanical properties of the weld, and enhance the overall integrity and durability of the welded joints. By subjecting the welded material to specific heating and cooling cycles, PWHT helps minimize the risk of weld cracking, distortion, or brittleness, which can result from the welding process.
NDT techniques, such as radiographic testing, ultrasonic testing, or magnetic particle inspection, may be employed to assess the effectiveness of the PWHT process and ensure that the welded joints meet required quality standards. Incorporating PWHT as part of NDT practices is essential in industries such as petrochemical, power generation, and construction, where welded structures are subjected to high temperatures, pressures, and structural loads. Proper PWHT helps ensure the integrity and safety of welded components, prolong their service life, and mitigate the risk of premature failures, making it a critical step in the welding and fabrication processes across various industrial sectors. This treatment is crucial in industries such as oil and gas, power generation, and construction, where welded structures are subjected to high stresses and harsh operating conditions.